As The Vomela Companies’ production teams and equipment relocate to their newly constructed St. Paul headquarters, they recently moved their state-of-the-art Box On Demand system. The machine gives employees the capability to configure cardboard packaging in any size and quantity, and it has replaced the need to order and stock a large variety of box sizes.
The system creates several efficiencies, which can then be passed on to clients. In the warehouse, the flat-packed cardboard can be stored effectively, and boxes don’t need to be created until there’s a need for them. It also reduces corrugate costs overall – each box is sized specifically for the job with minimal waste. These savings are reflected in shipping costs with the absence of void fill on trucks.
From a sustainability perspective, the machine has vastly improved Vomela’s waste reduction efforts. With 200-1,000 boxes produced per day, we’re using less cardboard and filling more space. What waste does occur is 100% recyclable cardboard scrap, which can be compacted and disposed of sustainably. With each box filling less space, we can complete orders with fewer shipments, which means less CO2 usage in the long run.
According to Material Prep Lead Don Andert, the system is reliable and easy to use. There’s no single operator of the on-demand system; user-friendly software allows any employee to create custom-sized packaging with the press of a button. With numerous benefits both sustainable and economical, it’s clear that on-demand box making is the future of packaging.
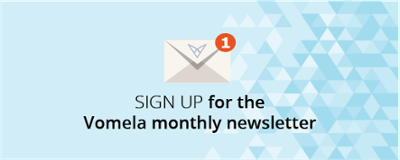